Porosity in Welding: Identifying Common Issues and Implementing Ideal Practices for Prevention
Porosity in welding is a pervasive issue that typically goes undetected till it triggers significant problems with the integrity of welds. In this discussion, we will check out the crucial factors adding to porosity formation, examine its damaging results on weld performance, and talk about the ideal methods that can be adopted to decrease porosity incident in welding procedures.
Usual Reasons of Porosity
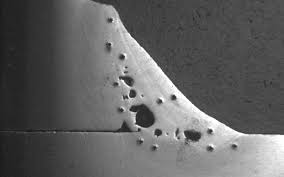
Making use of filthy or damp filler products can introduce pollutants right into the weld, contributing to porosity concerns. To alleviate these common causes of porosity, detailed cleaning of base metals, appropriate protecting gas option, and adherence to optimal welding parameters are essential methods in accomplishing top notch, porosity-free welds.
Influence of Porosity on Weld Quality

The existence of porosity in welding can dramatically compromise the structural integrity and mechanical homes of bonded joints. Porosity develops spaces within the weld metal, deteriorating its overall toughness and load-bearing ability. These voids act as tension concentration points, making the weld a lot more at risk to fracturing and failing under applied tons. Furthermore, porosity can minimize the weld's resistance to deterioration and various other ecological aspects, additionally decreasing its durability and performance.
Among the main repercussions of porosity is a decrease in the weld's ductility and sturdiness. Welds with high porosity levels often tend to show reduced influence toughness and decreased ability to warp plastically prior to fracturing. This can be specifically worrying in applications where the welded elements undergo vibrant or cyclic loading conditions. Additionally, porosity can restrain the weld's ability to efficiently transfer pressures, leading to premature weld failing and potential safety threats in vital structures.
Finest Practices for Porosity Avoidance
To boost the architectural stability and high quality of welded joints, what details steps can be implemented to lessen the event of porosity during the welding process? Utilizing the proper welding strategy for the details product being bonded, such as changing the welding angle and weapon setting, can better avoid porosity. Routine assessment of welds and instant remediation of any type of concerns identified during the welding process are necessary methods to prevent porosity and generate top notch welds.
Relevance of Appropriate Welding Techniques
Carrying out correct welding methods is extremely important in guaranteeing the architectural integrity and high quality of bonded joints, constructing upon the foundation of efficient porosity avoidance actions. Too much warm can lead to raised porosity due to the entrapment of gases in the weld pool. In addition, making use of the proper welding specifications, such as voltage, existing, and travel rate, is important for accomplishing sound welds with very little porosity.
Moreover, the choice of welding procedure, whether it be he has a good point MIG, TIG, or stick welding, need to align with the particular requirements of the job to ensure optimal results. Correct cleansing and preparation of the base metal, in addition to picking the best filler product, are additionally essential parts of skillful welding techniques. By sticking to these best methods, welders can minimize the danger of porosity development and generate premium, structurally audio welds.

Checking and Quality Assurance Steps
Testing treatments are important to detect and stop porosity in welding, guaranteeing the toughness and toughness of the final product. Non-destructive screening techniques such as ultrasonic testing, radiographic testing, and visual inspection are commonly employed to identify possible issues like porosity.
Conducting pre-weld and post-weld inspections is additionally vital in maintaining quality assurance requirements. Pre-weld inspections entail confirming the materials, tools settings, and useful reference tidiness of the workspace to stop contamination. Post-weld inspections, on the find this various other hand, examine the final weld for any kind of flaws, consisting of porosity, and confirm that it meets specified criteria. Applying a detailed quality control strategy that consists of detailed screening procedures and evaluations is critical to decreasing porosity problems and guaranteeing the total high quality of welded joints.
Verdict
Finally, porosity in welding can be a typical issue that influences the top quality of welds. By identifying the typical reasons of porosity and implementing finest techniques for prevention, such as proper welding methods and screening procedures, welders can make sure excellent quality and reputable welds. It is important to prioritize prevention methods to reduce the event of porosity and preserve the integrity of welded structures.
Comments on “What is Porosity in Welding: Ideal Practices for Staying Clear Of Permeable Welds”